
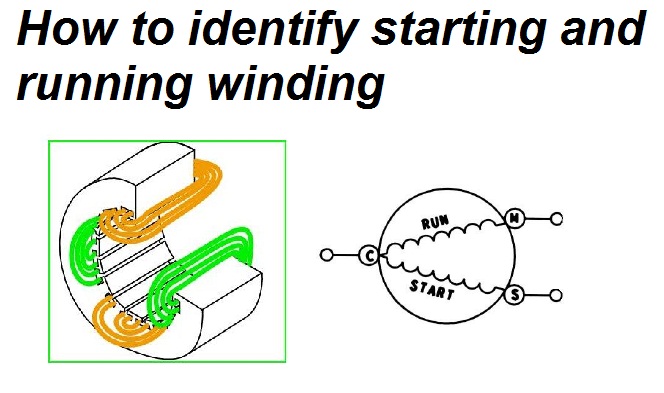
The sleeve part of the journal is keyed to the shaft and rotates with the shaft. This locks the rotor to the shaft for torque transmission but allows axial movement for thermal growth.Ī sleeve-type-bearing system provides the alignment and radial support for the long shaft and rotor assembly. The center bore of the rotor has an axial-keyway groove for engaging the axial key stock mounted on the motor shaft. This results in the "squirrel cage" rotor. Copper rotor bars are inserted into the lamination slots, the whole stack is compressed, and the rotor bar’s ends are mechanically bonded to the end rings. Rotors are constructed by stacking hundreds of thin, electrical-grade laminations between two metal end rings. Therefore, the rotors are constructed in short segments with radial support bearings placed between them for dynamic stability.

This would cause tremendous dynamic-instability problems because of the very large rotor length-to-diameter ratio.


Ideally, the rotor should be one continuous component that runs the length of the stator lamination bore. Its straightness is also critical because of its close rotating clearances and high speed. Typically, the shaft material is alloyed carbon steel. Because the shaft is completely immersed in clean oil, exotic corrosion-resistant materials are not required. The shaft is generally tubular material, and the hollow core allows for the motor oil to communicate from the motor head and base areas to the hotter radial bearing and rotor areas. The shaft transmits the torque produced by the rotors, keeps all the rotating components aligned axially, and provides a path for the cooling and lubricating oil to the radial bearings and rotors. The relationship of the HP, voltage, and amperage is Voltages range from 440 to 4,000+, and amperages typically range from 15 to 150+ amps. Typically, there are various selections running from low voltage/high amperage to high voltage/low amperage. Within each given length or HP, there are numerous voltage/amperage combinations. The length of the wound stator determines the number of rotors, which also determines the nameplate HP for a given-diameter motor. As its name implies, it is just a thin coating, mainly on the surfaces of the lamination slots and the mag wire, and has voids where motor lubricating oil accumulates, reducing both the thermal conductivity and the dielectric strength. The last two are less significant for the varnish coating method. And last, it protects the winding from an attack by contaminates such as wellbore fluid. Third, it significantly improves the overall thermal conductivity for better heat dissipation from the motor core through the slots to the motor housing skin. Second, it adds dielectric strength to the slot winding and end turns. First, it mechanically holds the windings to resist movement that causes wire-to-wire rubbing and possible damage to the wire’s insulation. This provides several important functions. The encapsulation process fills the voids left in the slots and around the end-turn coils. This protects for phase-to-phase faults.Īfter the mag-wire winding and insulation is complete, the wound stator is then encapsulated with either a solid-fill epoxy or varnish coating. Also, at the end of the lamination stack, where the coil has to make a 180° winding turn ("end turn"), insulation is placed between the first winding phase and the motor housing and then between each phase. The insulation on the mag wire provides wire-to-wire (turn-to-turn) electrical protection. Insulated copper wire called "magnet" wire or "mag" wire is then wound into each slot to form three separate phase coils displaced at 120° intervals. This slot insulation provides winding-to-stator (turn-to-ground) electrical protection. Each slot is insulated with a very-high-dielectric-strength polyamide insulation material. The laminations are die-punched with a center bore for the rotating components to fit into and 18 winding slots for the winding wire. The unwound stator has thousands of electrical-grade steel laminations stacked in the housing and is compressed to hold them aligned and stationary. A wound stator comprises an unwound stator, electrical windings, and insulation and encapsulation systems.
